content body
A country’s infrastructure is essential for the economy, environment and well-being of its people.
If you disagree, do you remember earlier this year when a cargo ship in Baltimore hit a support pier of the Francis Scott Key Bridge, causing a section of the bridge to collapse?
The bridge became impassable and almost all passenger and cargo shipping to the Port of Baltimore was halted, altering millions of lives and the national supply chain.
Researchers at Auburn University are dedicated to improving the nation’s infrastructure. The Samuel Ginn College of Engineering is home to the Auburn University Transportation Research Institute (AUTRI), which oversees cutting-edge transportation-related research within the college’s academic departments and research centers.
This includes the National Center for Asphalt Technology (NCAT) and its asphalt test track, the Highway Research Center (HRC), the Alabama Transportation Assistance Program (ATAP), Advanced Structural Engineering Laboratory (ASEL) and the GPS and Vehicle Dynamics Laboratory (GAVLAB).

Research at Auburn’s National Center for Asphalt Technology has supported the infrastructure that has kept America’s highways moving for nearly four decades.
Where the rubber meets the road
Work at NCAT has supported the infrastructure that has kept America’s highways moving for nearly four decades. It was created to ensure the asphalt industry can deliver pavements that are durable, sustainable, quiet, safe and economical.
The 1.7-mile oval test track is comprised of 46 experimental test sections sponsored cooperatively by highway agencies and private industry on a three-year cycle. Throughout each cycle, loaded trucks generate 10 million equivalent single axle loads on the track. Since operations began, trucks have accumulated enough mileage to circle the Earth 440 times.
Test Track Manager Jason Nelson likes to say NCAT is “where the rubber meets the road” because it is where the research faculty and students create in a lab or classroom is put to the test in a real-world setting.
“We are creating tests and specifications to design more sustainable pavements that incorporate high levels of recycled materials,” he said. “States can integrate these tests into their design procedures to assess road performance, resulting in improved roads for drivers nationwide.”
On the surface, researchers watch for wear and tear. Deep cracks allow water to penetrate the materials, potentially damaging the road’s integrity. Below the surface, test sections equipped with strain gauges and pressure plates provide data to track pavement responses and refine pavement performance.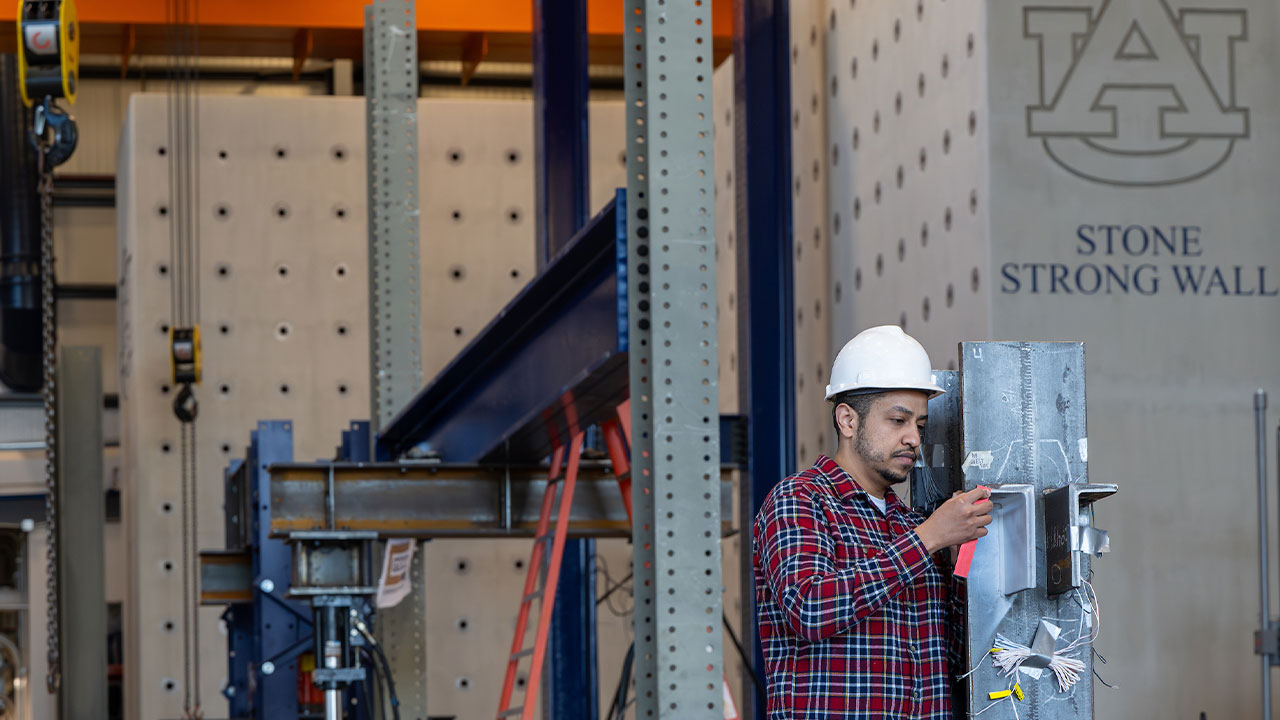
Research at Auburn’s Advanced Structural Engineering Laboratory supports state, federal and private industry projects involving the design, build and maintenance of steel, concrete and mass timber-produced roads, bridges and buildings.
Building better
Additional infrastructure research is applied at ASEL, specifically the design, build and maintenance of steel, concrete and mass timber-produced roads, bridges and buildings. At any given time, six to eight research projects are conducted for state, federal and private industry.
The 42,000-square-foot facility houses a high bay laboratory with a strong wall and strong floor specially engineered to handle extreme structural testing loads; a geotechnical chamber within the strong floor; a concrete materials research and testing laboratory; and wind testing capabilities that can replicate hurricane-level loads.
ASEL Director and Associate Professor Matt Yarnold, along with HRC Director and Mountain Spirit Professor Anton Schindler, currently lead a research project to evaluate the current performance of continuous bridge deck slabs for the Alabama Department of Transportation (ALDOT).
The team installed sensors on the slabs of a bridge in Livingston, Alabama, to measure stress caused by traffic and climate patterns. Back at ASEL, they are building a bridge section for testing.
If the team successfully develops enhancements to improve bridge performance, the changes could be used in most future bridges constructed by ALDOT.
“This is a small detail that can have a high impact throughout Alabama,” Yarnold said.

Four students in Auburn's College of Architecture, Design and Construction recently completed a project to design and build a home with only a 18x18 footprint, which is about the size of two parking spaces.
Building for the future
With the growing popularity of mass timber — the engineered wood product can be as strong as concrete and steel but weigh less — Auburn forged the Auburn Mass Timber Collaborative, bringing together experts in engineering, the College of Architecture, Design and Construction (CADC) and the College of Forestry, Wildlife and Environment.
Research and instruction in mass timber are conducted in several locations on campus, including ASEL, but also in west Alabama at Rural Studio.
A part of CADC’s School of Architecture, Planning and Landscape Architecture, the design-build studio challenges students to build with locally available, renewable materials and design to maximize energy efficiency and resiliency.
Four architecture students recently designed and built a home with an 18’x18’ footprint.